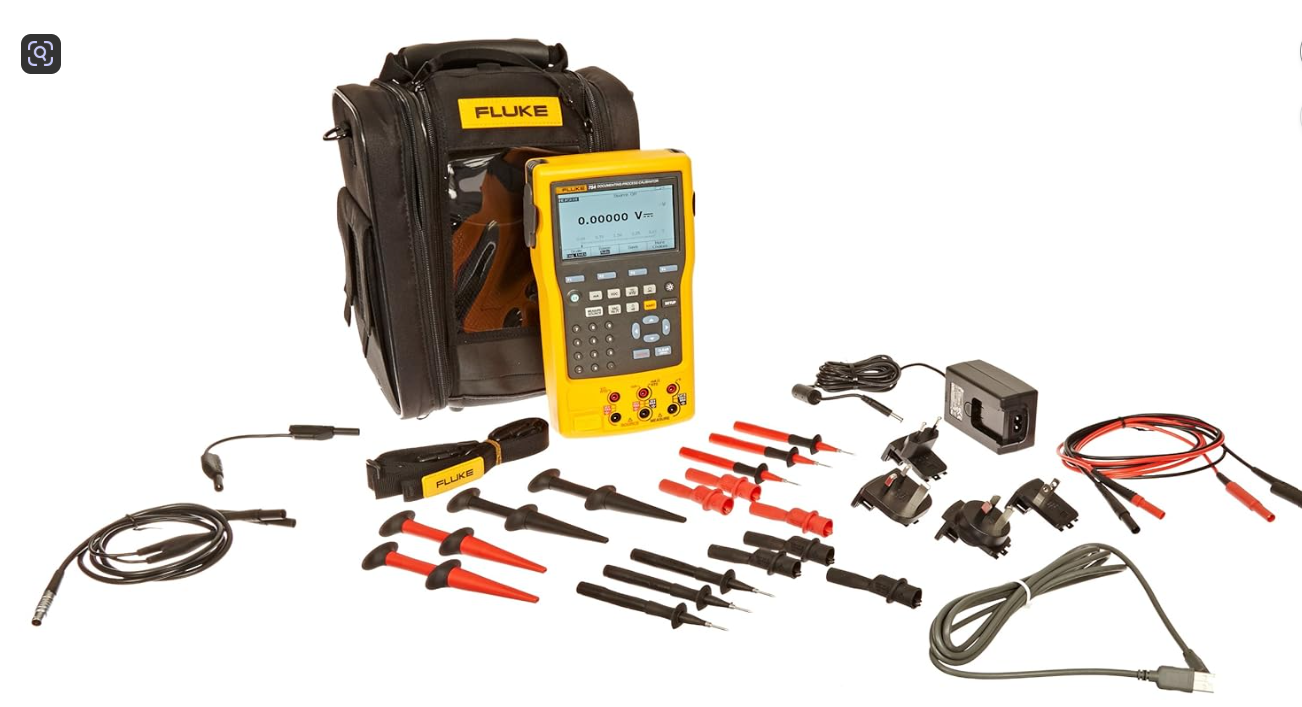
Understanding the Importance of Calibration
Lets talk about How to Calibrate Your Industrial Gadgets for Peak Accuracy. Did you know that inaccurate measurements can lead to a staggering 20% loss in production efficiency? Calibration is not just a technical nuance; it is a critical process that ensures our industrial gadgets deliver peak performance. Without proper calibration, even the most advanced equipment can produce unreliable results, costing us time and money.
If you click on our link to buy we will earn a commission with no additional cost
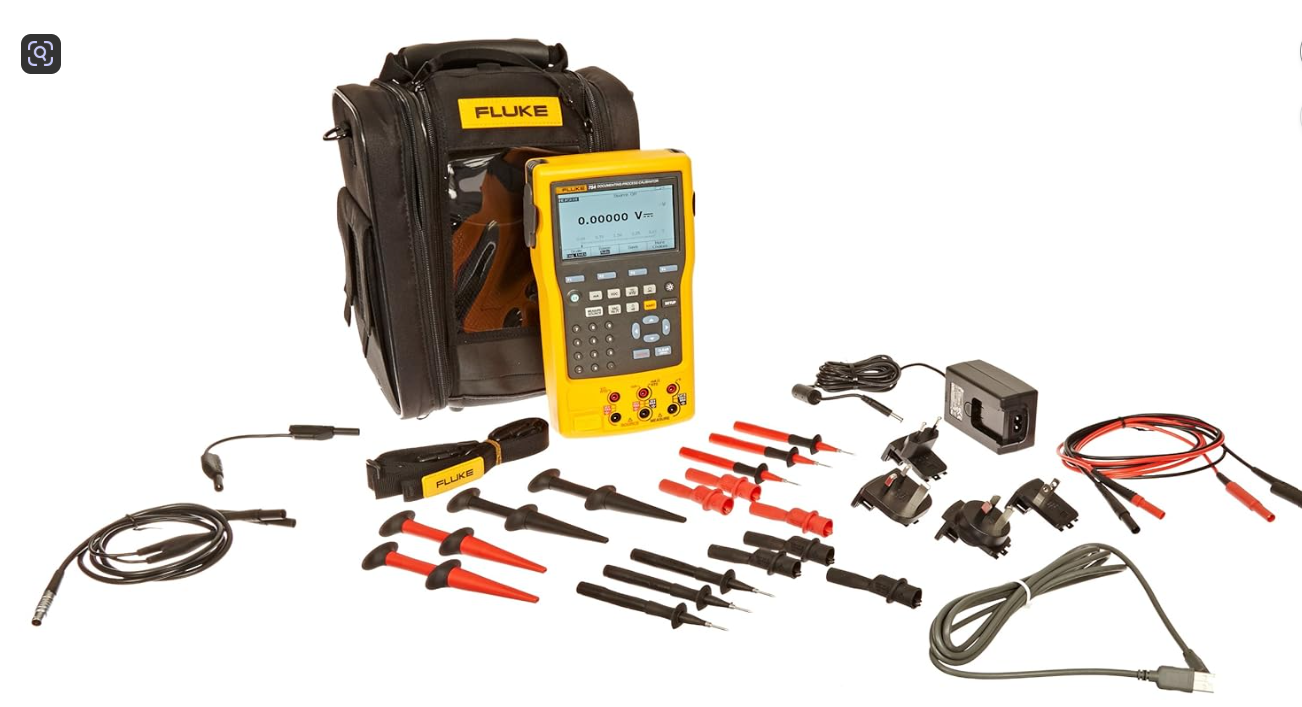
We often depend on our tools to provide precise measurements, whether it’s in manufacturing, quality assurance, or project development. When our gadgets are not calibrated, the reliability of our data and outcomes is compromised. This is where the importance of calibration comes into play. By regularly calibrating our equipment, we can maintain high standards of accuracy and efficiency, leading to enhanced operational performance.
In this article, we will dive into the essentials of calibration, explore the tools we need, guide you through the calibration process, and offer best practices for maintaining accuracy. Together, let’s ensure our industrial equipment runs at its best!




What is Calibration and Why is it Essential?
Calibration is the process of adjusting and verifying the accuracy of an instrument or device by comparing it with a recognized standard. Essentially, it allows us to ensure that our industrial gadgets provide reliable measurements, which are crucial for operational integrity and safety. This process is especially important across various industrial settings—from manufacturing to medical industries—where precision can directly impact product quality and compliance with regulatory standards.
Significance of Calibration
Proper calibration serves multiple key purposes:
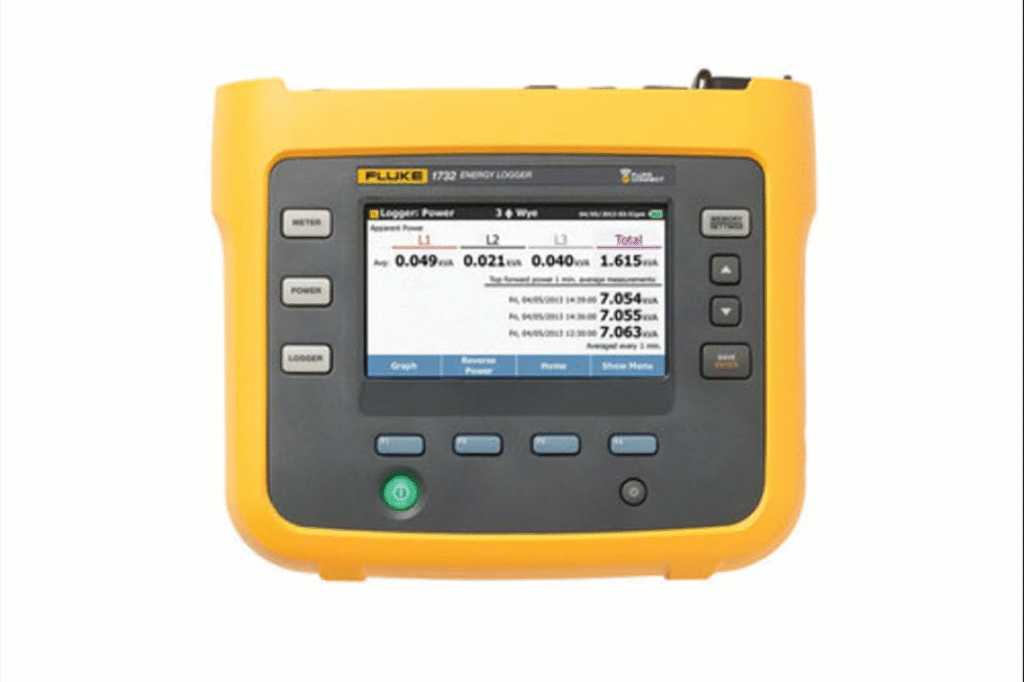
Real-World Impact
Consider a manufacturing plant that relies on pressure gauges. If these gauges are not calibrated, the machinery could either operate at dangerously high pressures or below optimal levels. Either scenario could lead to equipment failure, production downtime, or even workplace emergencies. Conversely, when we calibrate these gauges correctly, we ensure optimal operations, fostering a safer work environment and maximizing throughput.
Calibration Across Different Industries
The need for calibration isn’t confined to just one sector; it spans various industries:
Industry | Calibration Focus | Impact |
---|---|---|
Manufacturing | Dimensional measurements, pressure gauges | Prevents defects, increases yield |
Healthcare | Medical devices, lab instruments | Ensures patient safety, accuracy |
Food Production | Scales, pH meters | Maintains quality and compliance |
Aerospace | Navigational instruments, sensors | Enhances safety and functionality |
Construction | Surveying equipment, weight scales | Ensures structural integrity |
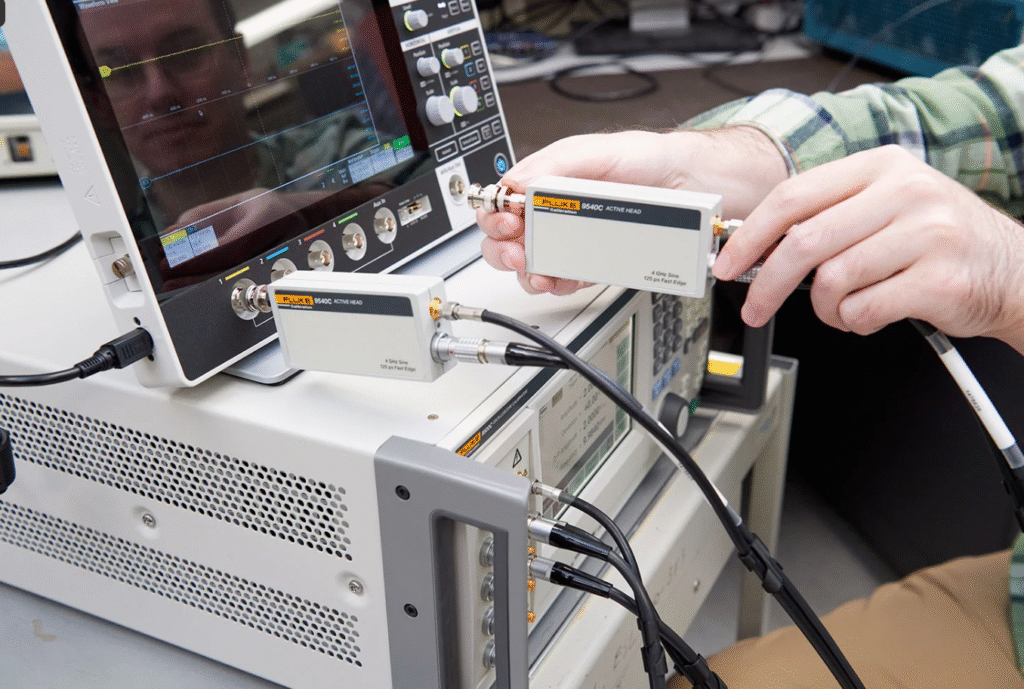
With these considerations in mind, it becomes clear that calibration is an integral part of our processes that directly influences our operational success. As we move forward, we will explore the essential tools and equipment required for calibration, crucial for maintaining the accuracy of our industrial gadgets.
Tools and Equipment for Calibration
In our journey towards achieving peak accuracy, we must arm ourselves with the proper tools and equipment for calibration. Each device plays a pivotal role in ensuring that our industrial gadgets deliver reliable results, and understanding their functions will help us make informed choices when performing calibrations.
Essential Calibration Tools
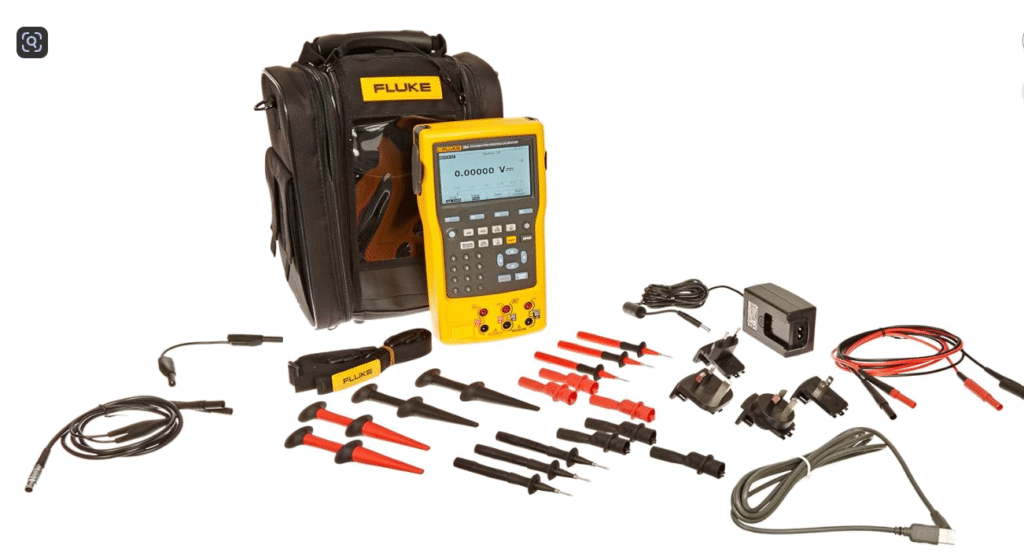
- Digital Calipers
- Digital calipers like the offer precise measurements for both internal and external dimensions. They are essential in manufacturing and engineering, allowing us to check critical dimensions of components quickly and accurately.
- Multi-Function Calibration Instruments
- These versatile tools can measure voltage, current, temperature, and resistance. They’re invaluable because they can handle various calibration tasks in one device, streamlining our calibration processes and minimizing the need for multiple instruments.
- Thermometers
- For industries where temperature control is crucial, such as food production and manufacturing, high-quality thermometers are a must. Calibration ensures that temperature readings are precise, helping maintain product integrity and safety.
- Pressure Gauges
- Regularly calibrated pressure gauges are vital in contexts like hydraulics and pneumatic systems. They help prevent equipment failure by ensuring that machinery operates within safe pressure limits.
- Weights and Calibration Masses
- Used to calibrate scales and balances, these weights ensure that we maintain accurate mass measurements. It’s critical for industries reliant on precise weight measurements, such as pharmaceuticals and food production.
- pH Meters
- In laboratories and food production, the accurate measurement of pH is essential. Calibrating pH meters with known buffer solutions allows us to obtain reliable readings that affect product quality.
Grouping Tools by Measurement Type
Measurement Type | Suggested Tools | Applications |
---|---|---|
Dimension | Digital Calipers | Manufacturing, Engineering |
Electrical | Multi-Function Calibration Ins. | General Electrical Testing |
Temperature | Thermometers | Food Production, HVAC Systems |
Pressure | Pressure Gauges | Hydraulics, Pneumatics |
Mass | Weights and Calibration Masses | Pharmaceuticals, Food Production |
pH | pH Meters | Labs, Food Quality Control |
Real-World Considerations
Imagine working on a high-stakes assembly line where even a slight deviation in measurements can result in product failure or safety issues. Having the right tools at our disposal allows us to promptly and efficiently calibrate equipment, mitigating risks and ensuring smooth operations.
Now that we understand the essential tools for calibration and their applications, it’s time to move forward and explore the step-by-step calibration process that ensures our industrial gadgets perform at their best.
Step-by-Step Calibration Process
Now that we’ve gathered our tools and equipment, it’s time to focus on the essential step-by-step calibration process. This is where we ensure our gadgets meet their specifications and operate at peak accuracy. Let’s walk through the preparation, execution, and verification steps together, while also being mindful of common pitfalls we should avoid.
Preparing for Calibration
Before we jump into calibration, we need to ensure we’re set up for success. Here are key preparation steps:
- Gather Your Tools: Ensure we have all necessary calibration tools at hand, as discussed earlier. This includes digital calipers, multi-function calibration instruments, and more.
- Check the Environment: Calibration does not occur in a vacuum. Factors such as temperature, humidity, and, potentially, background noise can affect measurement accuracy. Aim for a controlled environment when calibrating.
- Read Manufacturer Instructions: Each gadget comes with its unique calibration instructions. Familiarizing ourselves with these guidelines is crucial.
- Create a Calibration Schedule: Regular calibration should be part of our routine maintenance. Establishing a schedule based on usage frequency will help keep our gadgets in check.
Execution of Calibration
With our preparations complete, we can now execute the calibration process:
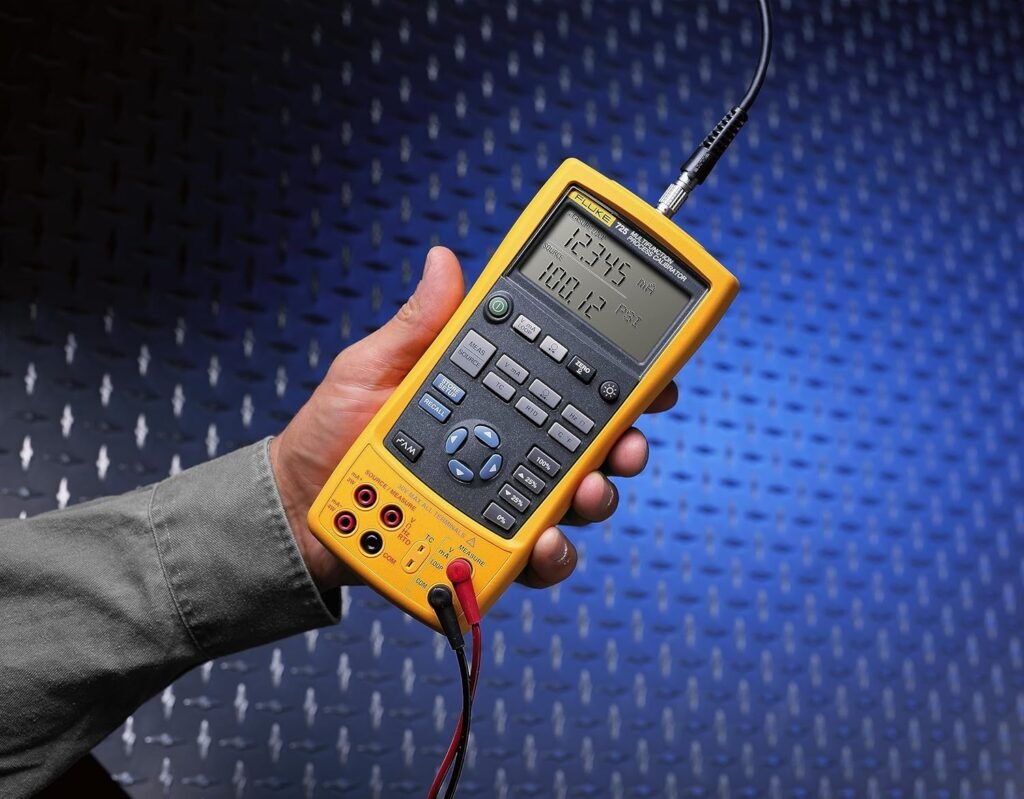
Fluke 725 Multifunction Process Calibrator
The Fluke 725 Multifunction Process Calibrator is a rugged, easy-to-use field calibrator designed for precision testing and calibration of a wide range of process parameters. With dual measure and source functions, it allows simultaneous viewing of input and output. It can measure volts, mA, RTDs, thermocouples, frequency, and ohms, and source/simulate volts, mA, thermocouples, RTDs, frequency, ohms, and pressure. Its compact, durable design makes it ideal for field use across various industrial environments.
- Set Up Calibration Standards: Start by connecting or positioning our calibration equipment in a manner specified by the manufacturer. For example, when using a digital caliper, ensure it’s zeroed out before taking any measurements.
- Perform Initial Measurements: Take baseline measurements with our gadget that is to be calibrated. This will serve as a reference point for adjustments.
- Compare against Standards: Use our calibration standards—precision weights, known voltage references, or temperature standards—to compare the measurements obtained. If our device shows discrepancies, adjustments must be made.
- Adjust the Equipment: Follow the manufacturer’s instructions to adjust settings until the gadget’s readings align with the standards. This could involve recalibrating dials, entering new values into software, or mechanically adjusting components.
- Record Measurements: Document all readings before and after adjustments. Keeping accurate records allows us to track calibration history and effectiveness over time.
Verification After Calibration
Now that calibration adjustments are made, verifying the results is crucial:
- Re-Measure Using Standards: After adjusting, use the calibration standards again to confirm that the gadget now provides accurate readings. This step ensures our adjustments were effective.
- Conduct Consistency Tests: Over a short period, take multiple measurements to confirm consistency. If variations occur, we might need a second adjustment or to investigate further to uncover underlying issues.
- Final Documentation: Update any calibration logs with the latest results, including the date, individual responsible, and notes on significant adjustments. Good documentation practices are essential for traceability.
Common Pitfalls to Avoid
While performing calibration, we need to be cautious of several common pitfalls:
By following this step-by-step calibration process, we can safeguard the accuracy of our industrial gadgets. As we refine our techniques, it’s vital to think about best practices for maintaining calibration over time to ensure sustained accuracy and efficiency, which we will delve into next.
Maintaining Calibration: Best Practices
As we continue our journey toward achieving peak accuracy in our industrial operations, maintaining calibration becomes an essential focus. Regular calibration isn’t just a one-time event; it’s an ongoing commitment that ensures our devices perform effectively over time. By integrating best practices into our routines, we can uphold the integrity of our measurements and safeguard our production processes.
Scheduling Regular Calibrations
One of the foundational aspects of maintaining calibration is creating a schedule for regular checks. We recommend a calibration frequency based on several factors:
Having a structured timetable not only ensures accuracy but also helps manage workloads efficiently.
Environmental Considerations
Our calibration accuracy can be easily compromised by the environment. Here are a few considerations:
These factors should always be part of our calibration strategy, contributing to sustained accuracy in our devices.
Training Staff on Calibration Procedures
We should never underestimate the value of training our staff on calibration procedures. Well-informed employees can significantly reduce the likelihood of calibration errors. Here’s how we can cultivate a knowledgeable team:
Empowered employees lead to improved accuracy and efficiency, making calibration a shared responsibility across the organization.
Documenting Calibration Records
Finally, we must emphasize the importance of meticulous documentation. Keeping thorough records of calibration activities offers multiple advantages:
By adopting these best practices for maintaining calibration, we can ensure ongoing accuracy in our industrial gadgets. As we refine our strategies, we must also be prepared to troubleshoot any calibration issues that arise, which is what we will explore in our next section.
Troubleshooting Calibration Issues
Despite our best efforts, calibration issues can occasionally arise, affecting the accuracy of our industrial gadgets. Recognizing the signs of inaccurate calibration and addressing them promptly is crucial for maintaining optimal performance. Let’s explore some common calibration challenges and how we can effectively troubleshoot them.
Signs of Inaccurate Calibration
When a device is out of calibration, it may exhibit several warning signs. Here are some indicators to watch for:
By being observant of these signs, we can act swiftly to prevent further discrepancies and maintain peak accuracy.
Common Calibration Issues and Solutions
Here are several prevalent calibration issues that we might encounter along with practical troubleshooting tips:
Issue | Possible Causes | Solutions |
---|---|---|
Inconsistent Readings | Environmental factors, vibrations, or power issues | Ensure a stable environment and proper grounding. |
Measuring Device Drift | Wear and tear; temperature variations | Perform regular calibrations and maintain a controlled environment. |
Calibration Equipment Faults | Damaged or dirty calibration tools | Inspect and clean equipment regularly; replace when necessary. |
Software Misalignment | Outdated or incorrect firmware/software settings | Update software regularly and review settings routinely. |
User Errors | Lack of training or unfamiliarity with tools | Conduct training sessions and provide easy-to-follow guides. |
Practical Troubleshooting Steps
Should we suspect calibration issues, follow these actionable steps to resolve them effectively:
Reassess Calibration Standards: Begin by verifying that our calibration standards are functioning correctly. Utilizing multiple standards can help isolate the issue.
Recalibrate the Device: If discrepancies persist, perform a recalibration following the prescribed methodology. Ensure all steps are followed meticulously.
Inspect and Clean: Look for any physical obstructions or grime on the measuring device and calibration tools. A simple cleaning can sometimes restore accuracy.
Evaluate Environmental Conditions: If the problem recurs, check the calibration environment. Implement measures to reduce vibrations, prevent temperature fluctuations, and eliminate dust.
Consult Manufacturer Documentation: Reference the manufacturer’s guidelines for troubleshooting. They may provide specific advice tailored to our devices.
When to Seek Expert Assistance
If calibration issues persist despite our efforts, it may be time to bring in a professional calibration service. Experts can provide advanced diagnosis and solutions beyond our regular scope, ensuring our equipment returns to peak performance.
By recognizing the possible challenges and implementing systematic troubleshooting strategies, we can tackle calibration issues effectively and keep our operational accuracy on point. As we enhance our understanding of resolving calibration discrepancies, we move confidently toward achieving peak accuracy through calibration, solidifying our commitment to quality and precision.
Achieving Peak Accuracy Through Calibration
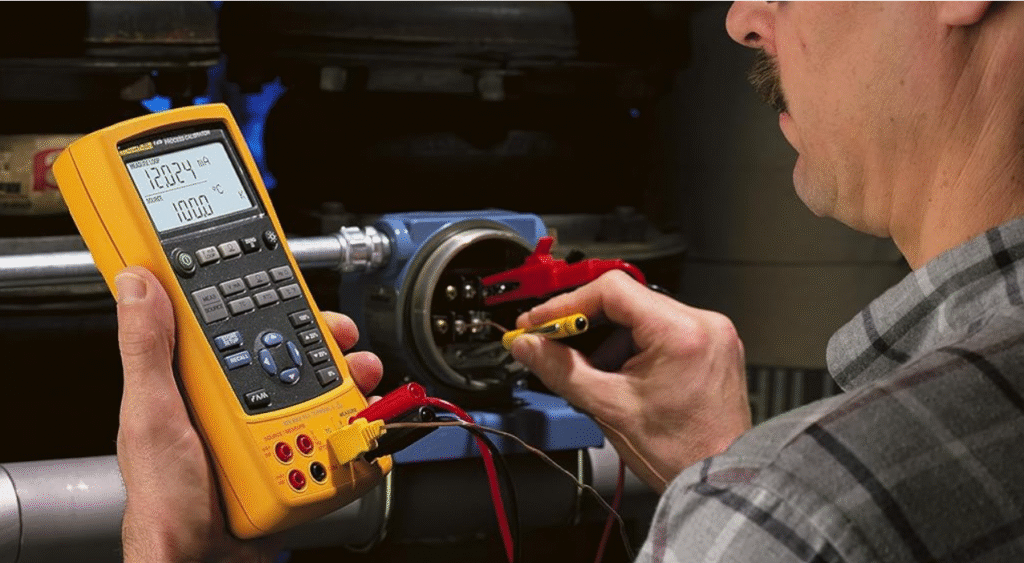
Credit Fluke.com
As we wrap up this exploration of calibration, it’s important to reflect on how these processes not only enhance the accuracy of our devices but also contribute to the overall success and safety of our operations.
Achieving Peak Accuracy Through Calibration
In conclusion, we have explored the vital role of calibration in maximizing the accuracy of our industrial gadgets. Regular calibration not only enhances the reliability of our measurements but also contributes to overall operational efficiency. We’ve covered essential tools, a step-by-step process, and best practices to maintain our calibration efforts.
Now, let’s take proactive steps to implement these practices and address any calibration issues. By doing so, we ensure that our equipment remains precise and effective. Let’s commit to a routine calibration schedule, adjusting as necessary, and embrace the pursuit of peak accuracy together. Remember, accuracy isn’t just a goal—it’s a necessity for success!
I guess calibration isn’t just a one-time thing? 🤯 I never maintained mine properly. Thanks for the tips on best practices!
Exactly, Nina! Regular maintenance is essential for peak accuracy. Glad you found the tips helpful!
Wow, I had no idea calibration stickers existed! Just ordered the Self-Laminating Calibration Stickers for my workshop. Hope they stick around for a while! 😂
Nice choice, Cathy! Those stickers are super convenient for keeping track of your calibration dates.
I use those stickers too! They’ve saved me so much hassle. Good luck with them!